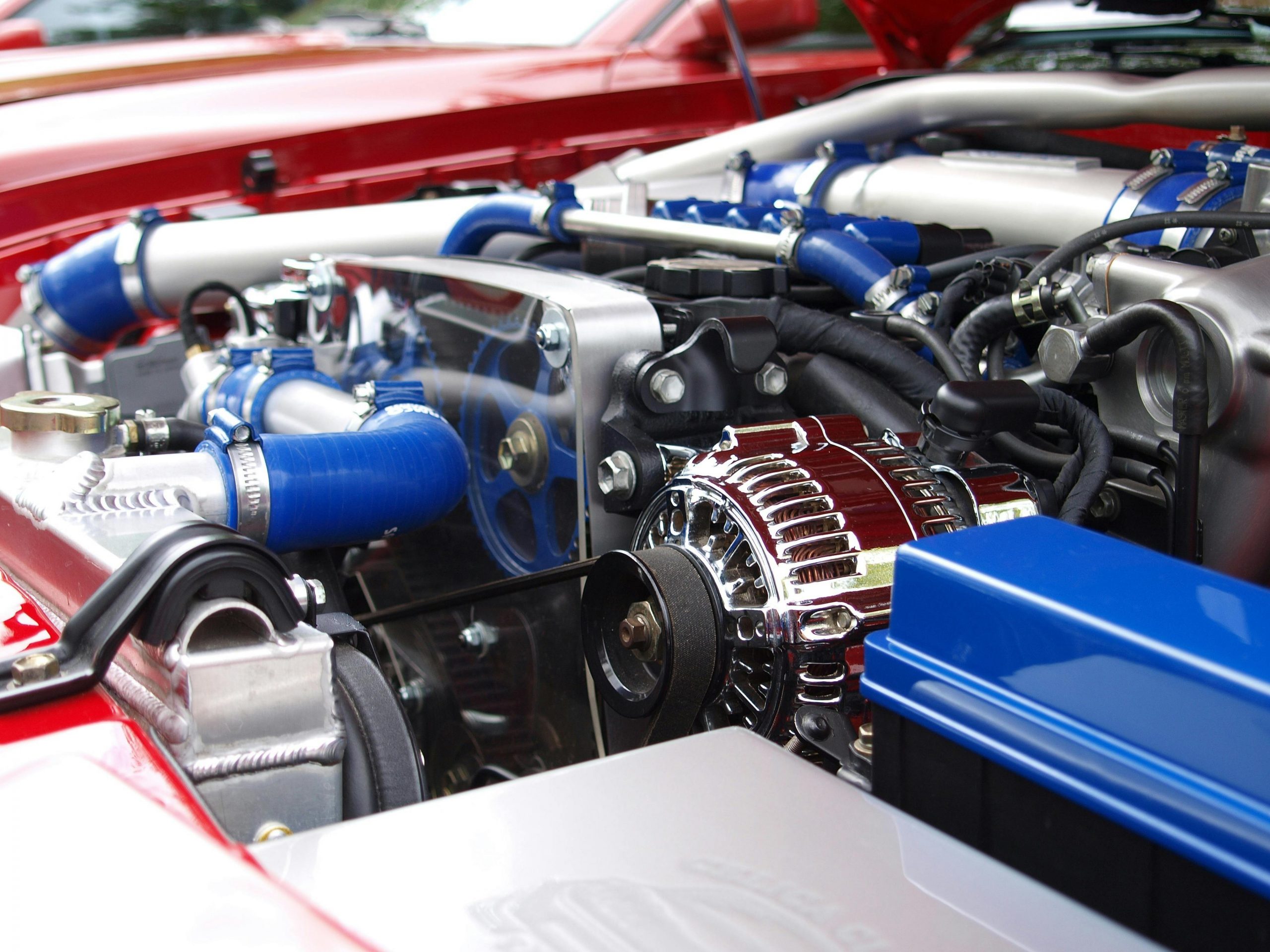
Automotive
A B2B case from Continental producing car dashboards
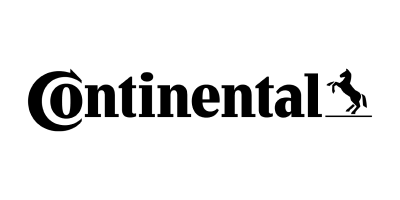
The Continental Automotive plant in Brandýs nad Labem is a global supplier of automotive electronics for many global brands with nearly 2,500 employees. In addition to modern production facilities for electronics and mechanical fuel transport units, the plant also has its own plastic moulding and
painting shop, where parts for part of the electronic production are created. The site also houses an R&D centre with its own sample room, which works on product development not only for Brandýs but also for other Continental plants around the world.
Background & Motivation
In the automotive industry, the so-called Call-offs or Forecasts are used to specify
the required deliveries. These are reports that provide an outlook over a longer period and are thus the basis for
the planning of production and purchasing. At the same time, the call-offs can change over time. They are
constantly being refined as the delivery date approaches. An abrupt change in the call-off may also occur because
of so-called immediate need whenever the car company is short of components that it must obtain as soon as
possible, otherwise the continuity of production is threatened.
For proper production planning, dispatch, and invoicing, it is important to be able to process these reports and to pass the data on to other systems so that the end result meets the customer’s requirements. Interconnecting the whole supply chain containing logistics, various
suppliers, and manufacturers into one ecosystem may significantly reduce the reaction time needed to satisfy the
changes in the call-offs and to adapt the production to such changes quickly. Additionally remanufacturing can
optimize the whole production also with respect to handle disruptions caused by insufficient-quality assemblies