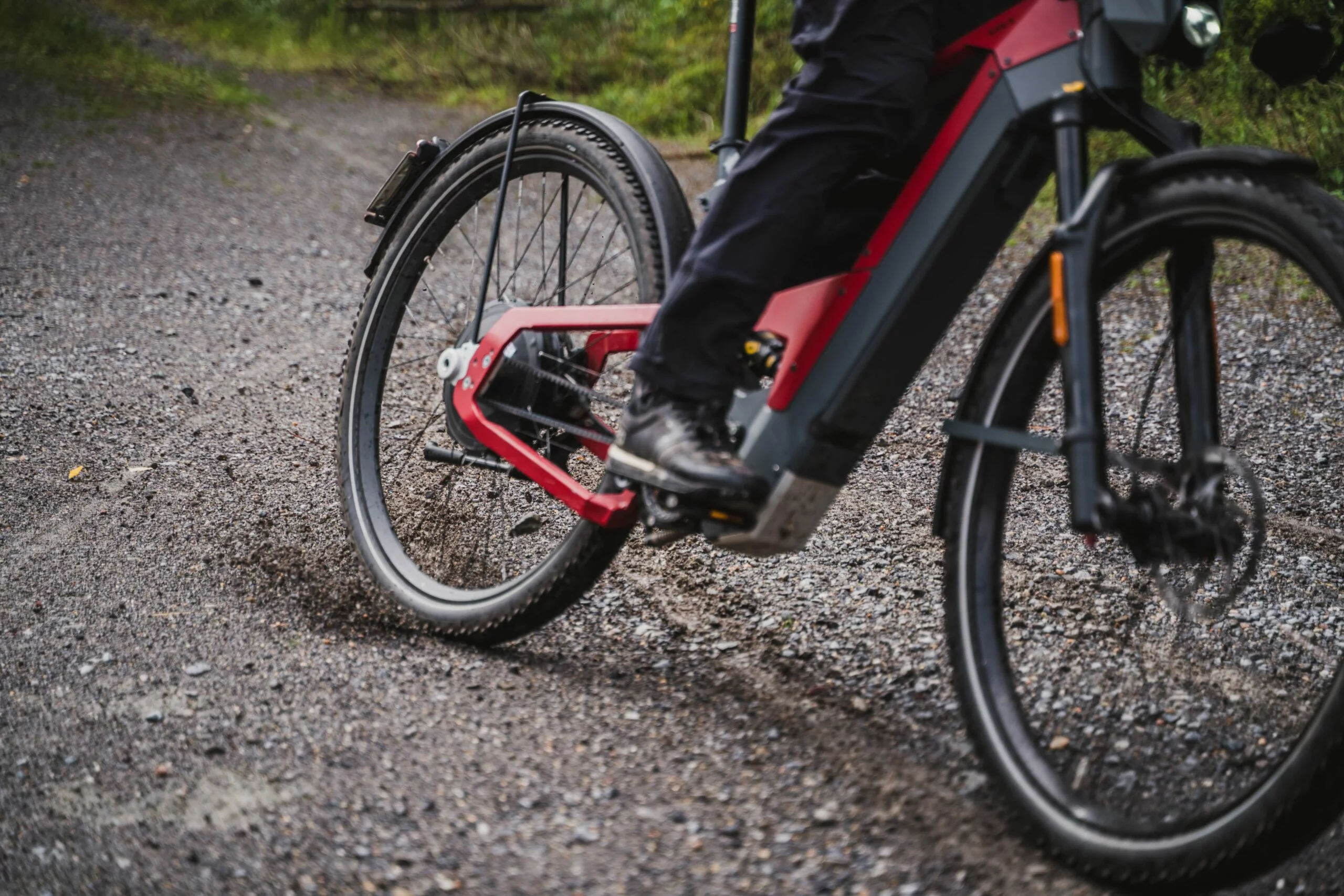
Bike Industry
A B2C Use Case From ÅSKA BIKE Producing Pedelecs
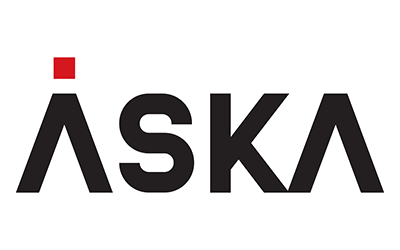
ÅSKA BIKE is an innovative Belgian speed-pedelec manufacturer with a strong focus on sustainability and resilience. To achieve this, a large part of its (direct) supply chain is situated in Europe.
Background & Motivation
Biking is taking an increasingly important role in Europe. However, the European bike industry is also suffering from unforeseen events that cause a disruption to bike production. This was for example the case with spiking demand of bikes during the Covid-19 period. To deal with these disruptions, the bike industry has a lot of potential to apply resilience mechanisms.
Bike producers not exclusively but often operate within following context:
- No manufacturing operations: A bike producer does not perform any manufacturing, neither of components, nor assembly. All manufacturing and assembly operations are outsourced. The bike producer can indirectly influence manufacturing by design for manufacturing, or by providing exchanging the right information to manufacturers.
- Few suppliers: A bike producer can have access to single suppliers for many of their crucial manufacturing steps, e.g., frame manufacturing, assembly. They need access to new suppliers and more flexibility in their supply chain. There is a need for quick quotations and procurement.
- Fluctuating demand: A bike producer sells to bike stores which place preorders. The e-bike industry is prone to fluctuations in demand due to disruptive events, high dependence on large component suppliers, and seasonal demand changes.
- Make to order: A bike producer may follow a Make to Order production technique, which is otherwise atypical in the bike industry. This allows them to be financially robust but creates a direct dependency on suppliers for on-time delivery. They need alternatives in the supply chain.
- Product with long lifetime: Customised bikes are designed with high quality and long lifetime in mind. There is an opportunity for lifetime extension. It might make sense that bikes will be IoT connected in the future with the opportunity to track their use and their state of health.
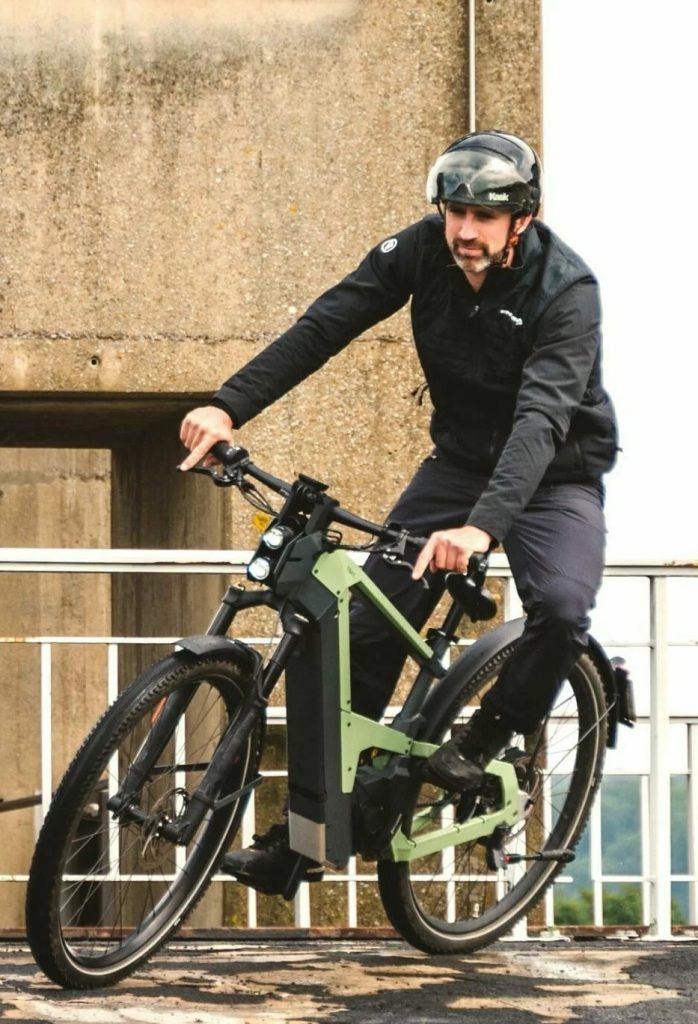
Challenges and Unforeseen Events
- Supplier cannot (temporarily) deliver – Delays or suspensions of deliveries due to internal disruptions.
- Market disruption – E.g. epidemics or pandemics like covid, geopolitical events and recession.
- Changing demands in the bike industry – Difficult to predict consumer trends on products with long life like bikes/new EU regulations for specific components
- Shortage of suppliers/long lead times in supply – Limited known suppliers, causing heavy dependency (single source) and inability to quickly source materials from elsewhere.
- Long lead times for receiving quotations – Suppliers take longer than expected to provide price quotes, slowing down procurement planning.
Goals of the Use-case
Different bike components require different resilience strategies.
OEMs can:
- Custom-design and on-demand produce critical parts with partners.
- Stockpile readily available, low-cost parts.
- Utilize remanufacturing for vulnerable parts like motors, creating a circular supply chain.
Flexible production rate
- Easily introducing second source to be able to adapt to fluctuating demand over the year
- Find potential suppliers in a network of alternative suppliers
- Fast way to get different quotations in a short time base on a digital product description
- Compare possible industrial partners to be able to quickly determine who will fill the order
- Evaluation tool for quotations
- Testing platform with suppliers
- Ability to change a supplier without the need for homologation of a new supplier
Product digital twin available to hand over to supplier
- Determine the best way to share tooling/fixture for suppliers (digital and/or physical) and to share information without the need for an NDA before sharing technical drawings.
- Understand the level of detail on which to impose the manufacturing process to (frame) supplier: from product oriented information to process oriented.
- Supplier now does the entire industrialization to make a quote.
- Ability to split up the production process to collaborate with different partners (each step to be monitored as a single product by the network).
- Track lifecycle data of individual bikes through a DPP to determine remanufacturing actions.