Research Challenges tackled by RAASCEMAN
Nowadays, the European manufacturing industry is facing multiple challenges: Increasing international competition, political tensions, material shortages or unpredictable natural events. These have exposed the weaknesses of traditional, rigid supply chains. The ability to adapt flexibly to changes is becoming a decisive success factor for manufacturers and suppliers.
RAASCEMAN addresses these challenges and is dedicated to the question of how supply chains can be made resilient and resistant. RAASCEMAN tackles the challenge of short-term and medium-term unforeseen events in a MaaS network enabling the human decision makers to react adequately by quantifying the impacts of those unforeseen events as well as providing possible alternative strategies.
RAASCEMAN helps MaaS networks handle unexpected disruptions like supply chain issues:
- Strategy 1: Adapt production plans and inventory levels.
- Strategy 2: Source parts from alternative suppliers within the MaaS network.
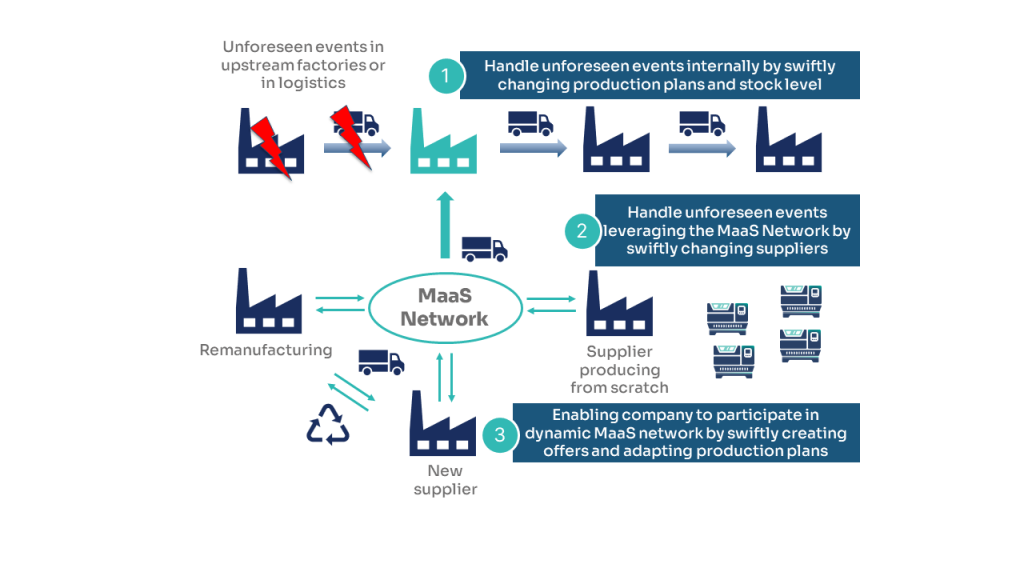
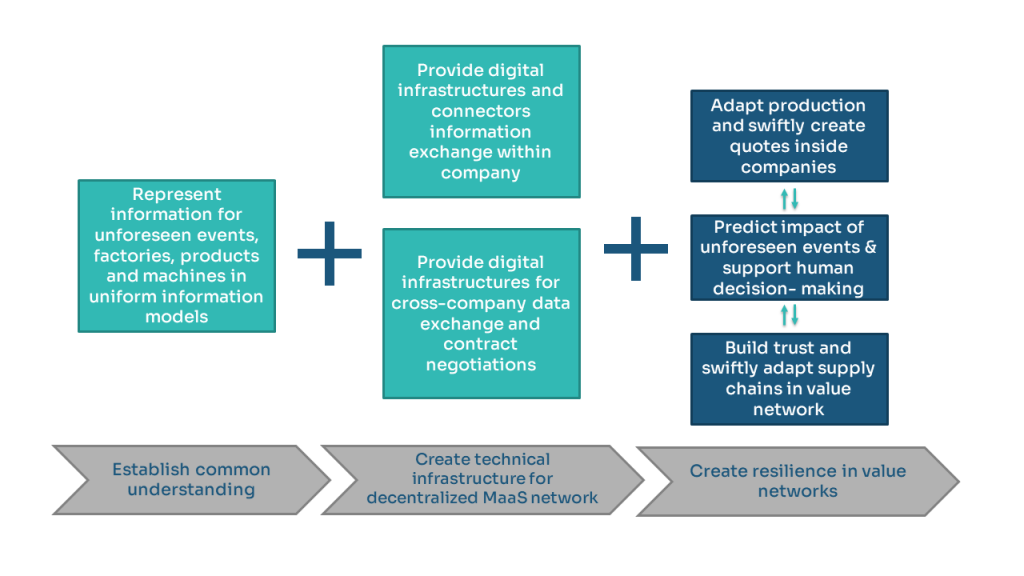
Concept and Approach
There are different possibilities for the procurement of parts. Either there is a supplier producing the required parts from scratch or else remanufacturing of parts is a suitable procurement, especially for high-quality products with a low number of suppliers. Both strategies can also be combined to tackle unforeseen events.
The foundation for enabling companies to participate in a dynamic MaaS Network is a common understanding which will be provided by defined semantics for the product digital twin as well as for factories and machines and unforeseen events.
Challenge: Common Semantic Representation
RAASCEMAN requires a technical infrastructure for data exchange between companies, enabling decentralized service provision and partial automation of negotiations. This infrastructure allows RAASCEMAN tools to interact, fostering resilience and flexibility in value networks. By predicting the impact of unforeseen events, companies can quickly adapt their production or supply chains. A decision support tool provides human decision-makers with the necessary information and alternative strategies to effectively respond.
RAASCEMAN tackles the challenge of transferring information about unforeseen events, products, factory services and machine capabilities within a MaaS network. Standardised and integrated software components using a common semantic representation are a prerequisite for intra- and cross-company communication and transparency across the MaaS network. In the project, semantic representations will be developed for the interoperability of software components, semantics-based information processing and human decision-making.
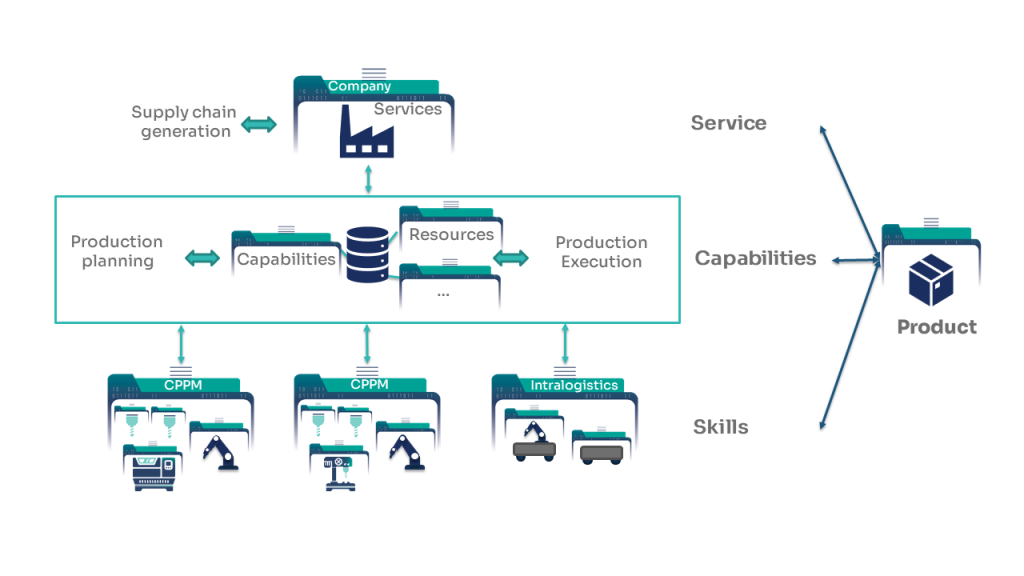
Challenge: Intra- and Cross-factory Communication Based on Standards and European Values
RAASCEMAN tackles the challenge of intra- and cross-factory communication by enabling trusted data exchange based on standards and according to European values. That includes clear specifications of interfaces and a modularized system architecture. To enable connectivity from the machine up to the MaaS Network several different standards and communication protocols must be provided by the digital platform and the middleware. This includes mechanisms for the registration and discovery of manufacturing services as well as vertical integration.
The platform leverages Asset Administration Shells (AAS) for intra-company infrastructure, providing a central hub for deploying and interacting with AAS for processes, resources, digital twins, and ERP systems. For inter-company communication, the platform implements GAIX-X interfaces (IDS/EDC) to enable secure and interoperable data exchange across supply chains while respecting data sovereignty.
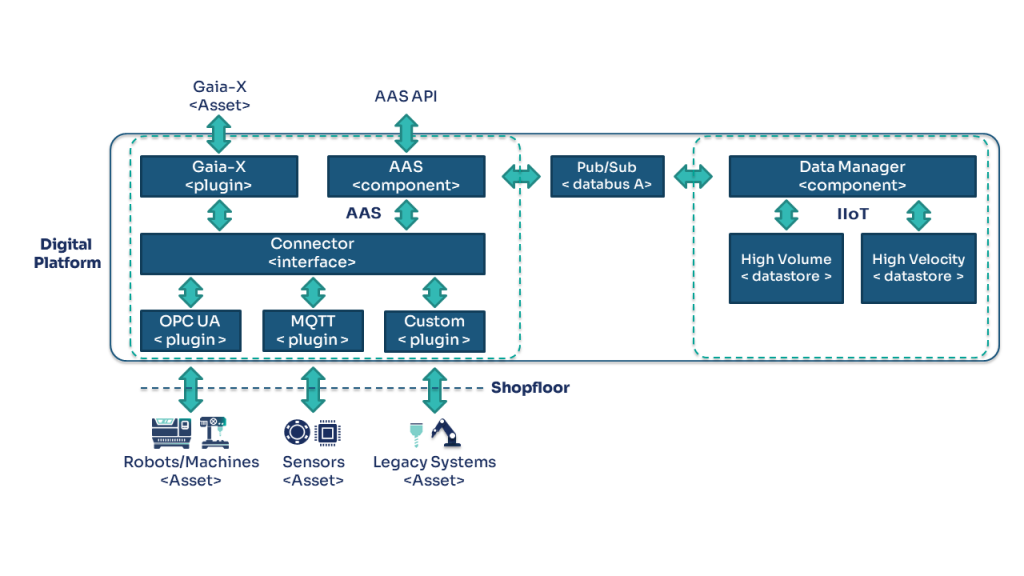
Challenge: Enabling Human Decision-maker to React to Unforeseen Events
RAASCEMAN addresses the need for informed decision-making in the face of unforeseen events in manufacturing. To remain resilient and flexible, manufacturers must dynamically adapt to fluctuations in demand, raw materials, and logistics. This requires the ability to predict and evaluate the impact of unforeseen events on their resources and processes across the entire value chain. Decision-makers need timely access to a variety of data and knowledge sources to make the best decisions, which can be complex depending on their role in the network.
To enable human decision makers to make informed decisions in case of short- and medium-term unforeseen events first a prediction of probability and impact of the unforeseen event is required. Additionally, decision support is needed for developing mitigation strategies comparing possible alternatives to react to the unforeseen event
including the associated costs.
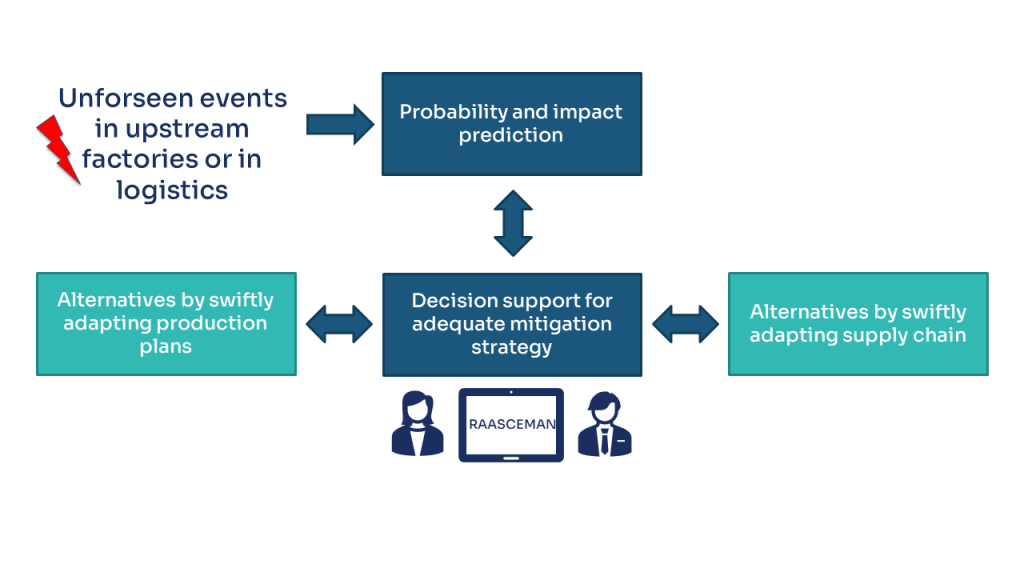
Challenge: Enable Companies to Swiftly Find Suppliers and Ensuring Trust and Reliability
RAASCEMAN tackles the challenge of facilitating the search for suitable suppliers and create trust in a decentralized MaaS network to enable the reaction to medium-term unforeseen events. In order to realise a trusted MaaS network, the selection and orchestration of suppliers in the network are of great importance. To select and coordinate the required suppliers, there must be a possibility to compare them against each other. However, the suppliers’ service descriptions need to be validated in a trusted MaaS network. The requesting company has to be sure that the supplier can guarantee the required quality of the product in case of unforeseen events.
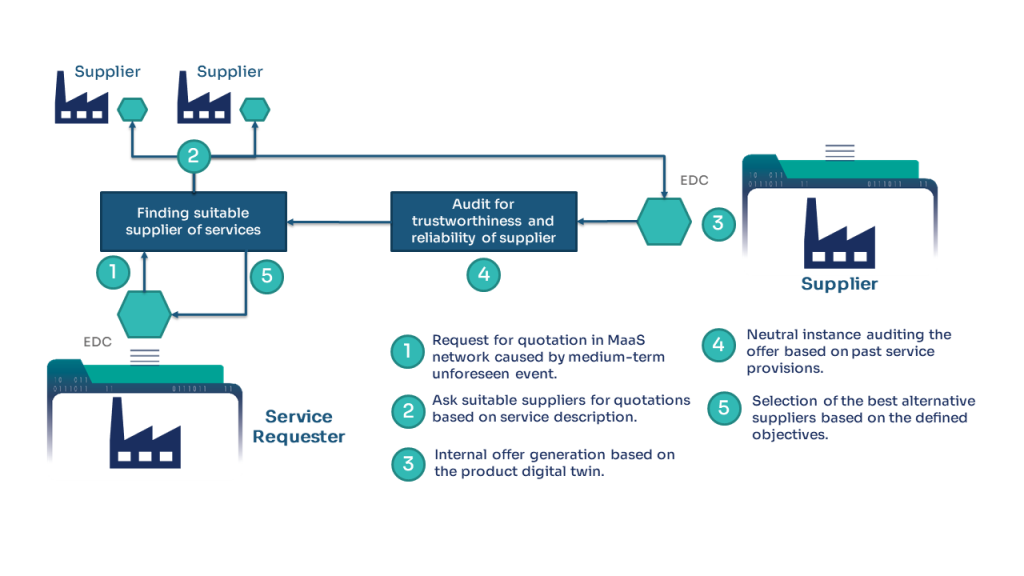
Challenge: Enable Companies to Swiftly Create Quotes and Adapting Production
RAASCEMAN aims to reduce time and effort in production planning, scheduling, and execution to respond dynamically to unforeseen events in the factory and enable participation in a MaaS network. These tasks are challenging, especially as complexity increases. In a MaaS network, companies must assess the technical feasibility of producing an unknown product with their equipment and map product requirements to machine capabilities to identify potential production plans. Organizational feasibility must also be validated, and production must be scheduled, considering KPIs like costs, delivery dates, and environmental impact, creating a multi-objective optimization problem. This project adds supply chain information, increasing complexity and impacting low-level optimization. To join a MaaS network, both production planning and execution must be more flexible, as current field-level processes are often rigid.
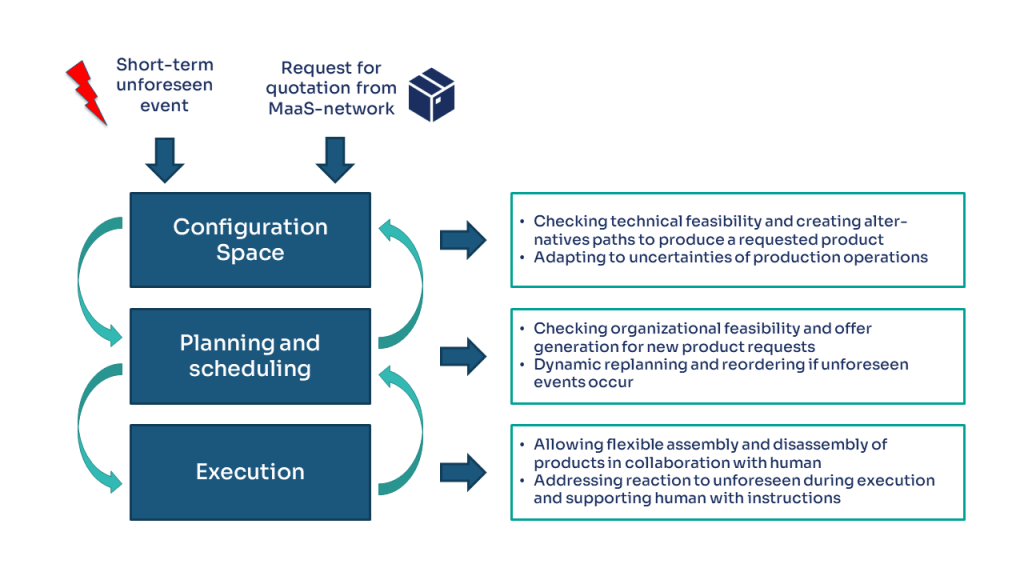
unforeseen events